March 16, 2018
News & Media
Best PPE(Personal Protective Equipment) Clothing
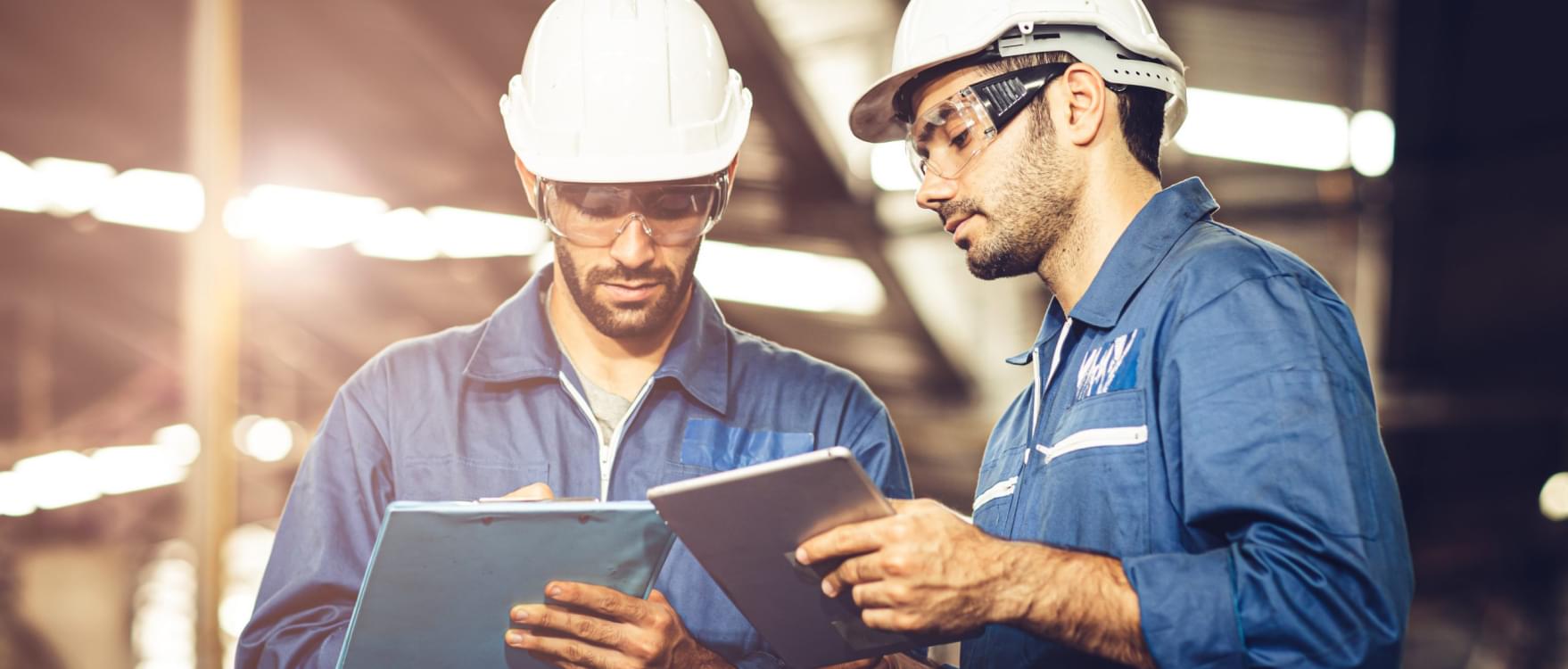
Too often in hazardous environments, the paradox of believing PPE (Personal Protective Equipment) to be the protection against all risks can do more harm than good. Although all risks cannot be eliminated from a dangerous workplace, hazard assessment can put a lid over most of the predictable risks by coming up with a suitable plan of actions. Typically, a workplace with high risk (high-risk) factors demands that employees coming into direct contact with the risky elements must wear suitable clothing for their jobs. However, it is important to remember that PPE is your last line of defense in the line of your duty and not the soldier in the front ranks.
The importance of wearing appropriate PPE cannot be stressed enough. Think of it this way: no one would even consider entering in a quarantine zone without a hazmat suit on. Likewise, personal protective equipment, regardless of its level of perfection, cannot protect employees unless they are using it per its intended purpose. The purpose of a PPE is to protect the employees from safety and health risks at work and to minimize the probability of physical harm. From helmets and footwear to ears/eyes protection and protective clothing, personal protective equipment varies from job to job depending upon the nature of the risks assessed. The primary responsibility of providing a perfect solution to employees rests with the employers, who need to be vigilant in terms of providing PPE that is not only in perfect condition but is also proper for the job at hand. In fact, it is one of the crucial prerequisites to ensuring the safety of their workers and abiding by the legal and ethical responsibilities of their business.
The predominant issue that has been detected in PPE, personal clothing, in particular, is the level of discomfort and inconvenience felt by its users. While employees may find uncomfortable protective gear to be tolerable for jobs that last a short while, it is not recommended for work that lasts longer than a few hours. Uncomfortable and problematic gear is more likely to distract the workers from the job at hand and can result in errors, injuries, and loss of efficiencies. Since prevention is better than treatment, experts emphasize that employers should implement a proactive approach to PPE usage and not rely on learning safety by accident. Hence, the need of the hour is to design personal clothing that fits perfectly to the body of the worker without invoking unease while serving its intended purpose.
It is important to remember that employers can take all the necessary precautions to create a secure workplace, any extraordinary event may still happen. However, most of the serious incidents can be prevented by educating and training workers about the risks and how best to avoid such scenarios, in addition to providing workers with a safety kit that has the primary purpose of protecting them at all costs.
Garments made out of Flame Retardant fabrics, in this regard, are the most dominant section of a safety kit in areas where heat and flames are potential risks or where welding is happening, as they provide almost 80% of the protection coverage to the workers against harmful elements of their workplace. Since the majority of employers abide by the standards of a dangerous working environment, striving to create a risk-free environment for employees, they are actively searching for FR fabrics that meet their specific requirements. The increasing need for protection has created an increased demand for apparel made out of Fire resistant cloth and has led to the emergence of several FR fabric manufacturers, providing a range of fabric options to the relevant safety or procurement manager to choose from.
The FR fabric supplier and the end user are usually not linked directly to one another as the end user prefers the final product to be in the form of a garment, instead of raw material. In general, the end user and the suppliers are indirectly linked through an intermediary, who keeps a record of the requirement of the end user and the products of the suppliers. As soon as the garment supplier finds a fabric supplier that meets the demands of the end user, he executes communication with both parties in order to come up with the right solution for the end user. In certain cases, the end user requires a particular product and forwards his/ her requisites to the garment supplier, who then communicates with the fabric manufacturers to develop the absolute fit for the protective clothing.
Evolution of Protective Clothing
Reviewing the historical events it is evident that personal protective equipment is not a new concept. Although referred to as different names throughout the history, PPE has existed in various forms and materials, however, it has always served the same purpose; i.e. to minimize the risk of physical harm for the user. From the use of armors and chain mail to cuirass and bronze helmets, soldiers have consistently used protective gear to minimize the risk of getting physical injuries. Over the years, the protective gear has been evolved to its refined form and is now referred to as personal protective equipment due to the diversity of job nature and the associated risks. Before the establishment of OSHA, PPE was an optional regulation to be followed by employers as their corporate social responsibility in the USA. However, it was declared as the mandatory requirement for all employers to abide by, where necessary, in the year 1970 which marked a new era in history whereby the protection of workers was officially considered of significance.
Consequently, protective clothing has become a topic of interest for the employers in order to provide protection to workers as demanded by the nature of the job. Most commonly, the recipient of PPE belongs to the industries of oil and gas rigs, mining, construction, foundries, and utilities. OSHA for the USA market is the predominant influencer in determining the parameters and guidelines to be incorporated in the Flame-resistant fabric in order to develop a product that meets the standard of protection.
For other regions like Europe, the following standards are generally required for Flame-resistant fabrics.
• ISO 11612,
• ISO 11611,
• IEC 61482
However, these standards are not constant, instead, revisions need to be made with every iteration of progression. The question of why safety standards need to be revised can be answered with ease. With the passage of time, either new aspects of safety are revealed with the use of PPE or certain shortcomings in the current versions are detected. The changes in standards and corresponding products in the market place are evolving as a result of changes in technology as well as safety-related legislation. All of these scenarios lead to the modified versions of these safety standards so that the probability of risks is minimized to an optimum degree. If we are not actively embracing the evolution of safety standards then it may lead to accidents, eventually resulting in a riskier environment for the workers.
How Same Standards Generates Different Fabrics & Varying Levels of Protection
The suitability of a Flame-resistant fabric is perhaps the most important deciding factor in terms of choosing the protective fabric/clothing, appropriate for your workers. Most of the employers share confusion in differentiating one fabric from another since all the fabrics are following the same standards. In reality, the difference lies in the level of protection offered by the workwear fabrics from fire, sparks, and flame.
The reason why the majority of the fabrics are able to certify these standards is because of the basic minimum requirement of the safety standards which is limited to 5 washes only for ISO norms. In addition to the physical aspects, considering the number of washes is particularly significant in protective fabrics as the essence of premium quality and high performance of an FR fabric lies in its performance after it has been washed multiple times. In terms of quality, Daletec has proved to be of premium standard as its fabrics have been documented for FR durability even after 200 washes and tumble drying.
Daletec 2017 – A glimpse to the future of Personal Clothing
The new race to become the pioneers in PPE has started with the saturation in the FR fabrics market as most of the articles have passed the same parameters for 11612 and 11611. Fabric suppliers are now shifting their focus on research and development of FR fabrics that not only pass the safety standards but also adds an “X” factor to it. Some of the prominent X-factors in this market being considered by market leaders to include maximum protection from fire, sparks, and flame and are available as light wear or comfort wear.
2017 has been a year of revolutionary success for Daletec as it has benchmarked in a number of new Fire-resistant / Fire Retardant articles, that have achieved high specs and offers the best protection even in super light weights. Through close partnership with our suppliers, best technical knowledge and deep analysis of ever-changing market demands, Daletec is responsible for introducing a number of groundbreaking articles to the personal clothing industry.
Within one year, three major developments in three different areas have been made by Daletec showing the extent of diversity offered by us.
1. TopSpark
Even with a superlight weight feature, and comfortable fabric, TopSpark has successfully certified to 11612 norms, which has been made possible only through Daletec’s innovative research and development.
Who would have thought it would be so easy to get hold of superlight shirting fabric in 180gsm, certified for 11612. The contradiction between fashion and PPE no longer stands correct as TopSpark has successfully bridged the gap by its vibrant color and fashion-with-comfort style.
2. GrindMaster
This Nano-tech development was made to consider the comfort of welders and grinders working in foundries, which are always looking for super light comfort wear to replace the existing heavy weight and uncomfortable garments of the welders.