April 15, 2020
News & Media
Introduction to NFPA and ISO Norms
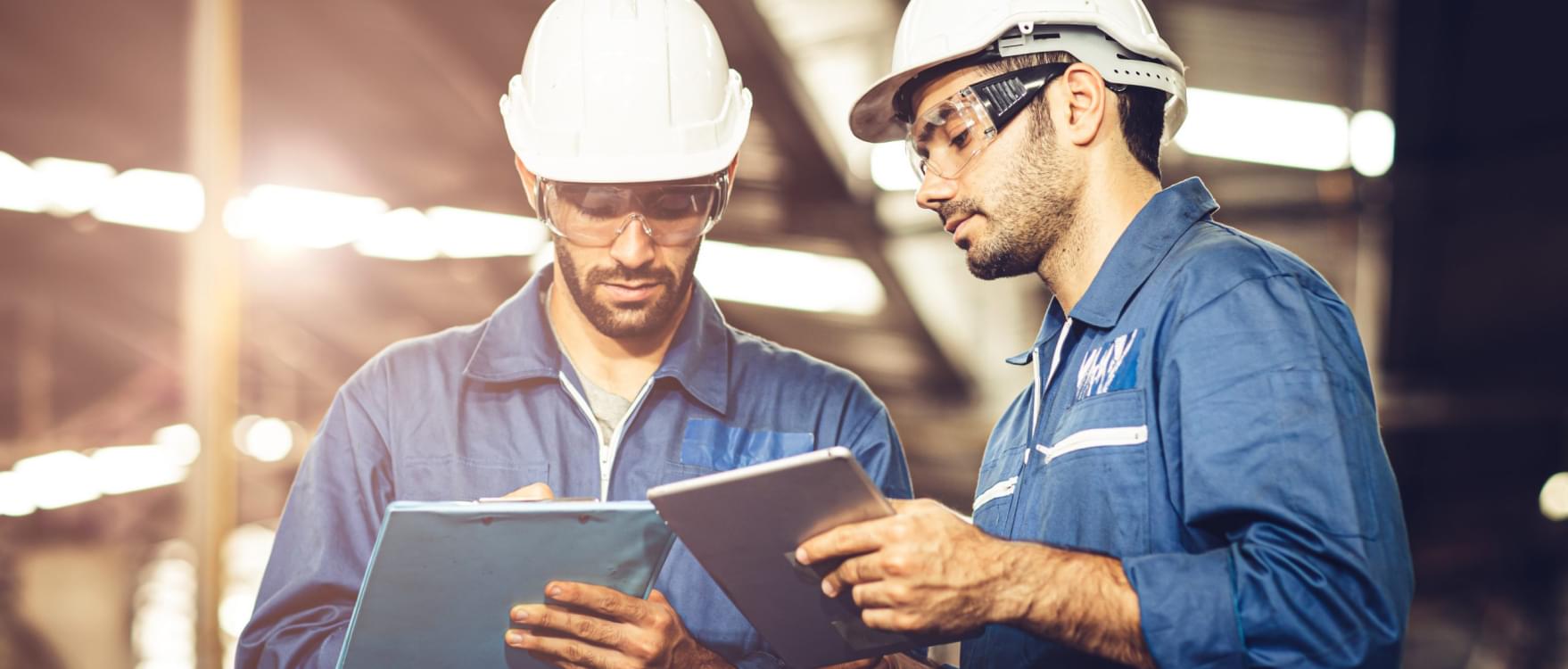
Workers’ safety is of utmost importance and there cannot be any compromise in equipping workers with appropriate PPE. Independent international organizations have been developing guidelines and standards for the health and safety managers to follow in order to ensure the quality of protective fabrics/clothing which leads to improved safety levels for workers.
In general, ISO norms are referred to check the quality and safety parameters of protective fabrics/clothing in Europe and the most of the world whereas NFPA standards are followed for USA.
Being the responsible producer of flame retardant fabrics, Daletec has always focused on the significance of PPE clothing. We are ISO 14001 certified company having highly talented professionals -with long experience -who are continually working on to bring out the best and environment friendly solutions for our esteemed customers.
The purpose of this article is provide better understanding of both ISO and NFPA norms and to highlight the key differences in these two standards as these norms are followed to check the quality and safety parameters of protective fabrics/clothing.
We have established unique processes, specialized innovative FR technologies by which we are producing flame retardant fabrics / heat resistance fabrics that provides protection against heat, flames, electrical arc and hot metal splash.
Let’s first discuss the NFPA norms.
NFPA (National Fire Protection Association) has dedicated its efforts to eliminate death, injury, property and economic loss due to fire, electrical, and other related hazards. NFPA is basically a nonprofit organization based in the United States formed in 1896. It promotes safety standards, education, trainings and support on fire and electrical hazard. NFPA creates standards and codes that are used by businesses, governments, and other organizations in order to improve fire safety. These standards protects workers from flash fire exposure and injury by specifying minimum performance requirements and test methods for flame retardant/fire retardant fabrics and garments.
PPE managers follow the NFPA norms with the intent of not contributing to the burn injury of the wearer, providing a degree of protection to the wearer, and reducing the severity of burn injuries resulting from short-duration thermal exposures or accidental exposure to flash fires.
NFPA 2112
Standard for Flame Resistant Clothing for Protection of Industrial Personnel against Short term thermal exposures from Fire.
This standard specifies the minimum performance required and test methods for Fire-resistant fabrics and the design and certification requirements for garments developed to protect workers from a flash fire hazard. It requires Fire-resistant fabrics to pass a comprehensive number of thermal tests including the following:
- ASTM D6413 – Vertical Flammability Test – maximum 2.0 seconds after flame and 4.0 inch char length.
- ASTM F1930 – Thermal Mannequin Test – maximum 50% predicted body burn after 3.0 second thermal exposure.
- ASTM F2700 – Heat Transfer Performance (HTP) test – minimum HTP of 6.0 cal/cm2 spaced and 3.0 cal/cm2
- Thermal Shrinkage Resistance – fabric must not shrink more than 10% after 5.0 minutes in a 260° C (500° F) oven.
- Thermal Stability Test – fabric must not melt or drip, separate or ignite after 5.0 minutes in a 260° C (500° F) oven. This is for fabrics and garments components not required to meet the Thermal shrinkage test.
NFPA 2112/2113 Standards
These standards specify design, performance, certification requirements and test methods for flame resistant garments for use in areas at risk from flash fires. Third party certification is required. NFPA 2112 sets a flame resistant requirement of less than or equal to 4.0 inches of char length damage.
- NFPA 2112 test exposure is set at 3.0 seconds.
- CGSB (Canadian General Standards Board) and NFPA define a flash fire as “typically 3.0 seconds or less.”
- NFPA 2112 sets failure above 50% of predicted body burn. For a garment to pass NFPA 2112 testing, it must exhibit 50% or less total predicted body burn using a standardized burn injury model.
- Under NFPA 2112 all flame resistant clothing must not melt, drip, or after flame in Flame Resistance test
Each fabric layer is required to be tested as received and after 100 cycles of washing and drying and/or dry cleaning.
Measure of how easy materials ignite and how materials burn. Once ignited, the after-flame must not exceed 2 seconds, and material shall not melt and drip.
Measure of fiber/fabric damage due to flame exposure. Char length must not exceed 102 mm (4 in.).
NFPA 2113 standard on Selection, Care, Use, and Maintenance of Flame-Resistant Garments for Protection of Industrial Personnel Against Short-Duration Thermal Exposures from Fire
Heat Transfer Performance (HTP)
The HTP is the amount of heat it takes to pass through the fabric to cause second-degree burns based on the skin burn curve. NFPA 2112 requires a fabric to have a minimum of 6.0 cal/cm2 when tested with a spacer and 3.0 cal/cm2 in contact and fabric shall not melt, drip, separate, or ignite after 5 minutes at 260C (500F).
Fabric must be tested both with the fabric specimen in contact with the sensor assembly and separated from the sensor by a ¼ inch spacer. A minimum TPP/HTP of 6.0 cal/cm2 is required for spaced and 3.0 cal/cm2 for contact tests.
ASTM F1506 – Arc Flash Method
Standard Performance Specification for Flame Resistant and Arc Rated Textile Materials for Wearing Apparel for Use by Electrical Workers Exposed to Momentary Electric Arc and Related Thermal Hazards.
This specification provides performance requirements for clothing worn by electric utility workers and other personnel working around energized parts. In addition to non-thermal requirements, the standard requires the fabric to be flame retardant. FR here is measured using ASTM D6413 Vertical Flame Test (maximum 2.0 seconds after flame and 6.0 inch char length). The arc rating is either Arc Thermal Performance Value (ATPV) (the energy on a material predicted (50%) to cause second degree burns) or Arc Break-open Value (EBT) (the energy on a material predicted (50%) to cause the material to break open (form holes)) which is measured by the ASTM F1959-06ae1 Arc Thermal Performance Test.
The standard has a general requirement that thread, findings and closures do not contribute to the wearer’s injuries in an electric arc exposure. Knit or woven fabrics may not melt and drip or have more than 2.0 seconds after flame or 6.0 inches char length. Arc ratings must appear on garment labels.
NFPA 70E
This standard addresses electrical safety-related work practices for employee workplaces. These safety measures are necessary for the practical safeguarding of employees relative to the hazards associated with electrical energy during activities such as installation, inspection, operation, maintenance and demolition of electrical conductors, electric equipment, signaling and communication conductors and equipment and raceways. This standard also includes safe work practices for employees performing other work activities that can expose them to electrical hazards.
NFPA 70E Requirements
The flame retardant fabric and garment requirements are those shown in ASTM F1506. Tables of common electrical tasks are included and assigned one of five Hazard Risk Categories (HRC 0, 1, 2, 3 or 4). Each HRC category has a minimum arc rating for protective clothing measured in cal/cm2 plus other PPE requirements.
Employers must use safe work practices and PPE which includes arc rated clothing based upon the incident energy associated with the specific task. Total system arc rating of layered ensembles must be determined by a multilayer arc test. If PPE is selected using the NFPA 70E tables, all layers used to determine the total system arc rating must be flame resistant. Employers must document an overall safety program including hazard/risk assessment and job briefing procedures which must be audited annually. For layered systems, arc ratings cannot be added together. Each ensemble must be tested layered as it will be worn. CSA Z462 is the Canadian standard for electrical workplace safety. As currently written, the PPE requirements are virtually identical to NFPA 70E.
PPE Category (HRC) |
Minimum Arc rating(cal/cm2) |
0 | Not Required |
1 | 4 |
2 | 8 |
3 | 25 |
4 | 40 |
ASTM F1959-14 Electric Arc Testing
Determines arc rating of materials based on electric arc exposure. Fabrics are mounted on flat panels for testing. Ratings are expressed in cal/cm2. Arc rating is reported as ATPV or EBT whatever is limiting the fabric being tested. ATPV is reported if the fabrics energy insulating is the limitation of the fabric. EBT if the material shows break open. None of the results of ATPV or EBT is better or worse than the other. The higher the value, the more burn protection.
This standard has a general requirement that it does not have any or pass/fail ATPV. 70E dictates what performance level is required based on risk assessment.
Introduction to ISO
ISO certification certifies that a management system, manufacturing process, service, or documentation procedure has all the requirements for standardization and quality assurance. ISO (International Organization for Standardization) is an independent, non-governmental, international organization that develops standards to ensure the quality, safety, and efficiency of products, services, and systems.
ISO certifications exist in many areas of industry, from energy management and social responsibility to medical devices and energy management. ISO standards are in place to ensure consistency. Each certification has separate standards and criteria and is classified numerically.
The ISO doesn’t have a set area of focus like the NFPA does. This allows them to create standards for a much wider range of things including testing and laboratory calibration, technical wiring and equipment, quality management, and much more. ISO do have fire safety standards that they publish, but unlike the NFPA, that is not their only area of focus.
Below is the brief introduction of ISO standards related to flame retardant fabrics.
ISO 11611 – Standard for Protective Clothing for use in welding and Allied processes
This Standard applies to clothing which is intended to protect the wearer against:
- Spatter (small splashes of molten metal) simulating various welding technologies
- Short contact time with flame
- Radiant heat from an electric arc used for welding and allied processes, and that minimizes the possibility of electrical shock by short-term, accidental contact with live electrical conductors at voltages up to approximately 100 V d. c. in normal conditions of welding.
- The ISO 11611 specifies minimum performance requirements for protective clothing designed to protect the wearer’s body based on two classes that reflect exposure to two levels of splashes. It does not cover requirements for feet, hands, face, and/or eye protectors. The garment is classified for the protection ability against different levels of welding technology, which cause more or less spatter and radiant heat.
- Class 1 – Protects against less hazardous welding techniques and situations, causing lower spatter and radiant heat
- Class 2 – Protects against riskier welding techniques and situations, which causes higher levels of spatter and radiant heat
EN ISO 11612 – Standard for Protective Clothing to protect against Heat and Flame
This International Standard provides minimum performance requirements for clothing used to protect the wearer’s body, excluding the hands, feet and head against heat and flame. This applies to clothing which could be worn for a wide range of end uses – where in addition to limited flame spread properties, protection is required against one of the following: exposure to, B- convective heat, or C- radiant heat, or D- exposure to molten metal Aluminum, or E- exposure to molten metal iron, or F- contact heat.
For each of the hazards listed in this Standard, there are 3 performance levels which indicate if exposure is low, medium or high risk. There is also a fourth performance level to takes into account for protection against extreme exposure to radiant heat. This level applies to high performance materials such as heat reflective aluminized materials. Within ISO 11612 there is an optional manikin flame engulfment test according to ISO 13506-1 and ISO 13506-2 with a recommended minimum of 4 seconds exposure. (Absolut minimum standard requirement is 3 sec)
Protective clothing certified according to EN ISO 11612 gives the wearer protection against brief contact with heat and flame. The heat can be convective, radiant, molten material, or a combination thereof.
The garment is classified for the following parameters:
- (A1) Limited flame spread
- (A2) Limited flame spread, hemmed specimens
- (B) Convective heat, scale 1-3 where 3 is the best
- (C) Radiant heat, scale 1-4, where 4 is best
- (D) Molten aluminums splash, scale 1-3 where 3 is the best
- (E) Molten iron splash, scale 1-3 where 3 is the best
- (F) Contact Heat, scale 1-3 where 3 is the best
EN 61482-1-2
PROTECTIVE CLOTHING AGAINST THE HAZARDS OF AN ELECTRIC ARC
Protective clothing certified according to EN 61482-1-2 (box test) protects the wearer against the hazards of an electric arc.
The garment is classified as follows:
Class | Arc [kA] | Time [ms] |
1 | 4 | 500 |
2 | 7 | 500 |
EN ISO 20471 – HIGH VISIBILITY CLOTHING
This International standard specifies requirements for high visibility clothing which are capable of visually signaling the wearer’s presence. The selection and use of high-visibility clothing should be based on a risk assessment of the conditions in which the wearer of the high-visibility clothing will be working.
EN 1149-3:2004 – Electric Discharge
Safety apparel where the surface material of the clothing is tested according to its electric discharge properties.
This standard specifies work wear that is tested for its ability to dissipate electrostatic charge from the surface of the clothing material.
The standard explains that the safety apparel has been tested for its ability to discharge electrostatic charges to the air and therefore won’t conduct it to the user of the clothing.
EN 13034 – PROTECTION AGAINST LIQUID CHEMICALS
Use the garment in combination with other garments providing protection as defined in EN 13034. Chemical protective suit (Type 6) shall cover and protect at least the trunk and the limbs, e.g. one-piece coveralls or two piece suits, with or without hood, boot-socks or boot-covers. Chemical protective suit (Type 6) forms the lowest level of chemical protection and is intended to be used if risks have been assessed as low and a full liquid permeation barrier is not necessary, i.e. when wearers are able to take timely adequate action when their clothing is contaminated. Low risks could be e.g. a potential exposure to small quantities of spray or accidental low volume splashes.
- Note that prolonged wearing of chemical protective suits may cause heat stress!
- All chemical protective clothing materials are tested and classified in accordance with Table 1. The construction of seams shall prevent penetration of liquid through stitch holes or through other components of a seam and not obstruct run-off of the liquid.
TABLE 1: PERFORMANCE REQUIREMENTS (EN 14325:2004)
Tests | Test method | Performance requirements |
Abrasion resistance | EN 530-2 | Class 1: > 10 cycles |
Trapezoidal tear resistance | ISO 9073-4 | Class 1: > 10 N |
Tensile strength | ISO 13934-1 | Class 1: > 30 N |
Puncture resistance | EN 863 | Class 1: > 5 N |
Repellency to liquids* | EN 368 | Class 3: > 95% |
Resistance to penetration by liquids* | EN 368 | Class 3: > 95% |
Conclusion
Both the NFPA and ISO have standards that apply to fire safety and prevention of injuries. These are not exactly the same standards however they have a lot of overlap. It seems clear that both organizations have tried to ensure that they are issuing the best practices that will help to improve safety whenever implemented. Therefore, it’s not surprising to see that some standards published by both ISO and NFPA are quite similar.
Both standards also have some basic differences e.g. washing temperature, number of washes which we have discussed above. Different chemical formulations can be used to quality ISO and NFPA.
Another difference between both ISO and NFPA is that both standards have a specific region where these are acceptable. For example, ISO standards are not widely acceptable in USA as they strongly prefer their fire retardant fabrics to be certified with NFPA standards. Similar is the case in European countries as they only accept ISO standards for fire retardant fabrics. In Asia, Africa, and Oceania mostly ISO standard are acceptable but also NFPA standards are used especially where US companies has big influence. In some regions they use the ISO or the NFPA standard depending on company policy.
ISO is a network of standards institutes from 164 countries with a central office in Geneva, Switzerland, that coordinates the system.
ISO is a non-governmental organization that forms a bridge between the public and private sectors and is the largest standards organization in the world. Many of its member institutes are part of the governmental structure of their countries or are mandated by their government. Some members have their roots uniquely in the private sector, having been set up by national partnerships of industry associations. Therefore, ISO enables a consensus to be reached on solutions that meet both the requirements of business and the broader needs of society.
One of common thing between the NFPA and ISO is that these are private standards organizations. This means that they don’t have any type of enforcement ability. Even that they have a long history of safety improvement, however, governmental organizations like OSHA (Occupational Safety and Health Administration) often adopt their standards, which are essential and are enforced by the government.
In the end, companies can greatly benefit by keeping up to date with all the recommendations put forth by both OSHA and NFPA. It will be quite rare to find situations where the two agencies issue contradictory recommendations, which means you can follow both to help maximize the safety of a given facility.